Welding Defects can be defined as the irregularities formed in the given weld metal due to wrong or incorrect welding patterns, etc. The defect may differ from the desired weld bead shape, size, and intended quality. Welding defects may occur either outside or inside the weld metal. Some of the defects may be allowed if the defects are under permissible limits but other defects such as cracks are never accepted.

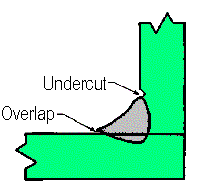
To avoid undercut, welder and welding inspector must observe initial weld lap to see whether the current setting is appropriate. Post welding inspection can be tricky since welder can cover undercut by running another lap using lower grade welding electrode and low current. Undercut is dangerous because it amplifies the stress flow due to reduction in section area and stress concentration of the notch form.

Troubleshooting Weld Defects
Like any portion of the manufacturing or fabrication process, the welding operation is subject to human error from time to time. When weld defects occur as a result of a problem with welding operator's technique or poor equipment settings, it can cause costly downtime and rework, not to mention, frustration.

When a weld defect appears, it's important for welding operators to have the knowledge they need to rectify the situation as quickly as possible. Faster troubleshooting leads to greater opportunities to add value to the welding operation — through increased productivity and quality improvements.



Undercut
Most structural failures originate from weld joint because it is the source of discontinuity or defects. The most visible weld defect we can easily find in visual inspection is undercut, shown in Figure 1 below. Undercut is usually due to overcurrent in electric arc welding. Overcurrent causes wide melting zone in base metal but not enough weld fusion metal to replace the gap. High lapping speed also leaves the gap poorly filled with weld fusion metal and produces undercut
To avoid undercut, welder and welding inspector must observe initial weld lap to see whether the current setting is appropriate. Post welding inspection can be tricky since welder can cover undercut by running another lap using lower grade welding electrode and low current. Undercut is dangerous because it amplifies the stress flow due to reduction in section area and stress concentration of the notch form.

Troubleshooting Weld Defects
Like any portion of the manufacturing or fabrication process, the welding operation is subject to human error from time to time. When weld defects occur as a result of a problem with welding operator's technique or poor equipment settings, it can cause costly downtime and rework, not to mention, frustration.
When a weld defect appears, it's important for welding operators to have the knowledge they need to rectify the situation as quickly as possible. Faster troubleshooting leads to greater opportunities to add value to the welding operation — through increased productivity and quality improvements.

Cold Cracks in Fillet Welds
VARIATIONS OF COLD CRACKS
Cold cracks are defined as cracks that occur at temperatures of 200-300°C or lower in carbon steel and low-alloy steel welds. Cold cracks can occur in both butt welds and fillet welds; however, this article will focus on those occurring in fillet welds.

No comments:
Post a Comment