laser beam machining
A laser beam machining device having aspherical lenses for uniformity of the cross section intensity of a laser beam emitted from a laser oscillator
,
and converging optical unit composed of a plurality of converging lenses disposed to be aligned in single or plural rows on a plane in the optical path of the uniform laser beam, whereby uniform machining can be performed in the middle and at the edges of the machining area and the allowable machining area can be made wider.

Laser Beam Machining (LBM) is a form of machining process in which laser beam is used for the machining of metallic and non-metallic materials. In this process, a laser beam of high energy is made to strike on the workpiece, the thermal energy of the laser gets transferred to the surface of the w/p (workpiece). The heat so produced at the surface heats, melts and vaporizes the materials from the w/p.Light amplification by stimulated emission of radiation is called LASER.
It works on the principle that when a high energy laser beam strikes the surface of the workpiece. The heat energy contained by the laser beam gets transferred to the surface of the w/p. This heat energy absorbed by the surface heat melts and vaporizes the material from the w/p. In this way the machining of material takes place by the use of laser beam.
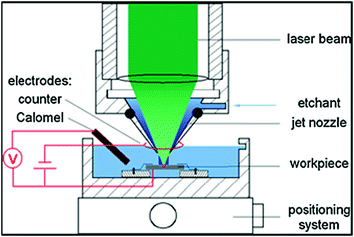
When talking about CNC shape cutting with typical cutting processes, kerf is the width of material that the process removes as it cuts through the plate.

A laser beam machining device having aspherical lenses for uniformity of the cross section intensity of a laser beam emitted from a laser oscillator
,

and converging optical unit composed of a plurality of converging lenses disposed to be aligned in single or plural rows on a plane in the optical path of the uniform laser beam, whereby uniform machining can be performed in the middle and at the edges of the machining area and the allowable machining area can be made wider.

Laser Beam Machining (LBM) is a form of machining process in which laser beam is used for the machining of metallic and non-metallic materials. In this process, a laser beam of high energy is made to strike on the workpiece, the thermal energy of the laser gets transferred to the surface of the w/p (workpiece). The heat so produced at the surface heats, melts and vaporizes the materials from the w/p.Light amplification by stimulated emission of radiation is called LASER.

It works on the principle that when a high energy laser beam strikes the surface of the workpiece. The heat energy contained by the laser beam gets transferred to the surface of the w/p. This heat energy absorbed by the surface heat melts and vaporizes the material from the w/p. In this way the machining of material takes place by the use of laser beam.
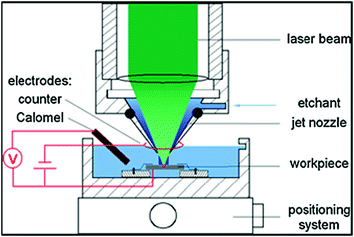
A high-quality, high-speed micromachining process is important for implementing a cost effective solution on a manufacturing machine. Use of lasers for micromachining has grown steadily over the years, and by 2015 laser micromachining is expected to be a $752M market.1 In recent years there also has been rapid advancement in laser technology. The energy available per pulse and the pulse repetition frequency (PRF) of diode-pumped solid-state (DPSS) nanosecond ultraviolet (UV) lasers have increased dramatically. Efficient use of the available energy from a laser source is important to achieve maximum material removal and minimal thermal damage for any laser micromachining application.
The use of the optimal energy density, or fluence (J/cm2), for material removal is especially important for short pulse-width lasers. Compared to longer pulse widths, a shorter pulse results in shallower thermal penetration depth, which means smaller heated volume and hence less residual heat-affected zone (HAZ) in the material.
This allows for a controlled and precise micromachining process, which is why many in the industry continue to choose short-ns pulse width DPSS lasers for their most quality-stringent applications.

Kerf = Width
Kerf is defined as the width of material that is removed by a cutting process. It was originally used to describe how much wood was removed by a saw, because the teeth on a saw are bent to the side, so that they remove more material than the width of the saw blade itself, preventing the blade from getting stuck in the wood.
Over the years I’ve heard some people use the term when referring to the angle on the edge of the part, but that would be an incorrect use of the word. The “cut angle” on the edge of the part makes measuring the kerf width sorta tricky, but for consistency, the word “kerf” should only be used when talking about the actual cut width.
No comments:
Post a Comment