DEFINITION :-
F Vollertsen, F Schmidt - International Journal of precision engineering …, 2014 - Springer
SHEET METAL FORMING AND MACHINING Our company acquired our first machine with computer-managednumeric control in the year 1996, and has constantly expanded in this area since then.Our trained specialists in production and our in-house design office can fulfill virtually all of your wishes.Using design illustrations or samples, we can create the workpiece that you desire from materials acquisition to the end product. Of course, we will also take care of a part of your production. Are you unable to perform a particular production step yourself, or do you not have the time? We can perform work for you in the areas of Flame cutting, welding, folding, rolling, turning, milling, tapping, deep hole drilling and sanding.....
F Vollertsen, F Schmidt - International Journal of precision engineering …, 2014 - Springer
In metal forming, lubricants are still used to prevent corrosion, to reduce friction, wear and
tool load as well as to protect the workpieces and intermediates. In economic and ecological
points of view, the challenge is the avoidance of lubricant usage. Within this article we define …
tool load as well as to protect the workpieces and intermediates. In economic and ecological
points of view, the challenge is the avoidance of lubricant usage. Within this article we define …

Improve machine efficiency
Metal Forming equipment operate under conditions of Extreme Pressure and Friction, causing a significant amount of wear to accumulate over time. This often results in noticeable decline in machine efficiency, excessive energy consumption and frequent breakdowns. Another issue is the inability to use wet lubrication in complicated manufacturing processes.
NanoLub® Anti Wear & Anti Friction lubricants are based on a unique patented technology of proprietary super strong tungsten disulfide (WS₂) multilayered nano fullerene-like particles. These unique multi-layer WS₂ nano-spheres lower friction and heat, thereby reducing mechanical wear. At the same time, contact pressure causes nano-spheres to release tribofilms that attach to surface asperities and smooth them, thereby extending mechanical efficiency and apparatus life. Nanolub® product range includes Extreme Pressure Oil and Grease AW/AF additives as well as AW/AF Dry Coating, capable of significantly improving the performance of Extreme Pressure applications used in the Metal Working industry

Progressive & Transfer Stamping Genesee A&B, Metal Forming is our core competency. It’s true that our team and facilities have expanded to include a variety of other services and solutions, but metal forming has been our foundation from the beginning and continues to be our focus. Our metal forming services have 2 main components that we would like to highlight: Progressive Stamping and Transfer Stamping. Our clients know us for reliability and tr ansparency, so we’d like to give you a look at how we work in both of these areas.
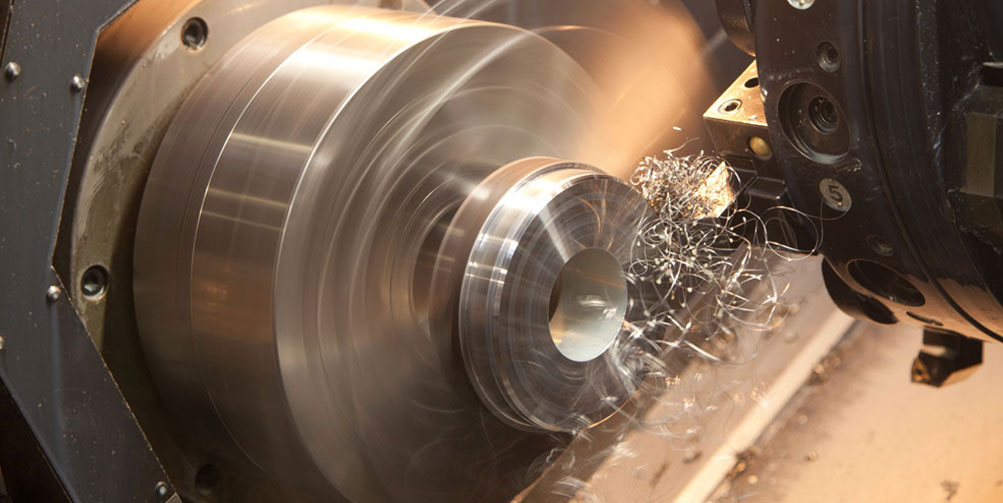
Utilizing Eastwood’s Metal Forming Tools - Pounding Metal Utilizing Eastwood’s Metal Forming Tools
During our visit at Empire Fabrication a couple issues back, we noticed the intricate rear suspension display that was currently in the works on a VW Caravelle van. Lots of intricate metal work was being done to cover the ’bags and mounts in the form of metal “blisters” or humps, so we stuck around for a quick metal shaping lesson.
With the use of assorted tools from Eastwood, Sean Ramage walked us through the process of forming, shrinking, pounding, and hammering metal in the name of custom fabrication, and shared a couple tricks along the way. Read up and take a few notes.
No comments:
Post a Comment